In the next 2~3 years, ESS battery cells will continue to upgrade to higher capacity, the cell capacity is expected to increase to more than 300Ah, which will put higher requirements on battery technology, production and materials.
For now, these ESS large battery cells are prismatic cells. According to the difference of cell assembly process, prismatic cells can be divided into two categories: stacked battery cells and wound battery cells.
So, what is the difference between stacked battery cells and wound battery cells?The following is battery electrode lamination & stacking process VS battery electrode winding process, showing the advantages and disadvantages of each.
The battery winding process has been developed over a long period of time and has the following advantages.
- The industry chain supporting the battery winding process is very mature and the investment cost is relatively smaller.
- Battery electrode winding technology is very mature, the battery electrode winding machine has been highly automated, and its production efficiency and yield rate are also very high.
As the cell capacity and size continue to increase, the disadvantages of the battery winding process become more apparent.
- Wound cells have curvature at the corners, resulting in lower space utilization than stacked cells, and the larger the battery capacity, the more obvious the space waste.
- Wound cells have curvature at the C-corners, and the cell is prone to wavy deformation, which will lead to poor battery interface and uneven current distribution, accelerating the decay of battery life.
- After the bending of the electrodes of the wound cells, the coating material undergoes large bending deformation, which will easily induce problems such as powder dropping and burring, and this will increase the risk of internal short circuit and thermal runaway of the battery. As the cell capacity and size continue to increase, the requirements of wound battery cells for battery manufacturers' extreme manufacturing will rapidly increase, and the difficulty of compatibility between high-capacity battery cells and the winding process will steeply increase.

Below are the features of the battery lamination & stacking process.
Firstly, the advantages.
- The number of battery tabs in stacked cells is twice that of wound cells. The increase in the number of battery tabs results in shorter electron transfer distance, 10%~15% lower resistance compared to wound cells, less heat generation, and longer theoretical cycle life, meeting the requirements of mass ESS for high safety and ultra-long cycle life.
- Stacked cells do not have the problem of C-corners in the process of cell assembly, which can make full use of the space at the corners of the battery shell and improve the volumetric energy density and mass energy density.
- The stacked cell does not have the problem of unbalanced internal stress in the C-corners, and each layer of electrodes can maintain a relatively flat interface during long-term cell cycling, avoiding problems such as uneven current distribution and better capacity retention in the middle and late cycle life.
However, for large-capacity battery cells, the battery lamination & stacking process has some disadvantages at present.
- The battery lamination & stacking process has been developed for a relatively short period of time, the industry chain is not mature enough and the investment cost is relatively higher.
- Battery electrode stacking technology has not been mature enough, the automation of battery electrode stacking machine is relatively low, and its production efficiency and yield rate are also relatively low.
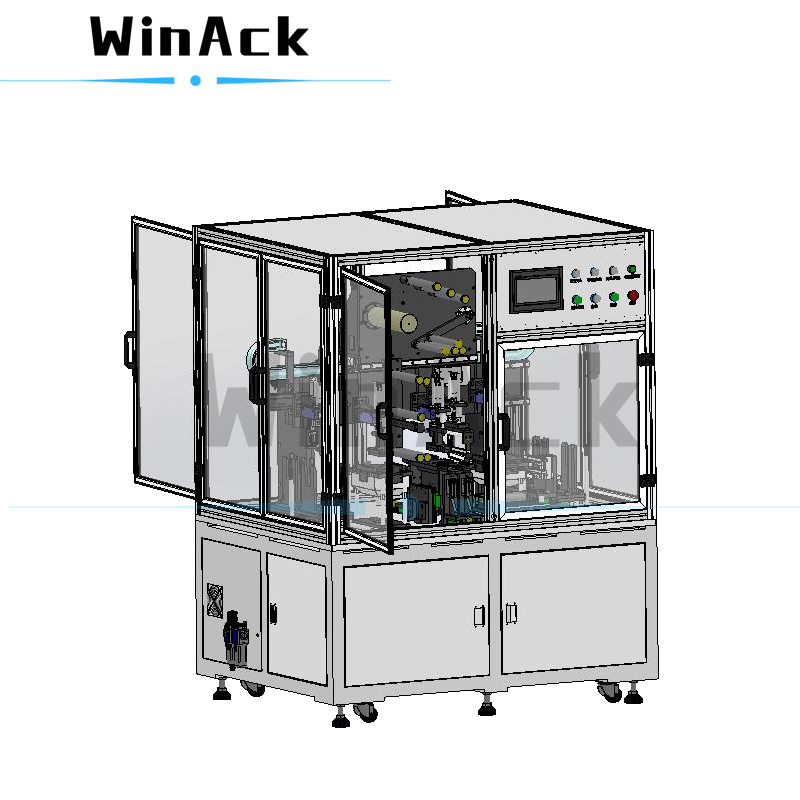
In summary, in theory, stacked cells have the advantages of higher volumetric energy density ceiling, more stable internal structure and longer cycle life, which is a better match for the production process of high-capacity battery cells, but there are shortcomings such as high equipment investment cost, low yield, insufficient efficiency and difficult process.
With the maturity of the battery lamination & stacking process technology and the improvement of the efficiency of the battery stacking machine, the low efficiency and high cost of the stacked battery technology is expected to be completely solved, and form a competitive situation of " complement and compete with each other with the battery winding process technology.
WinAck Group can provide full set of battery cell production line solutions. Come by, contact us for a solution that can help you succeed. For better batteries, Win & Ack!